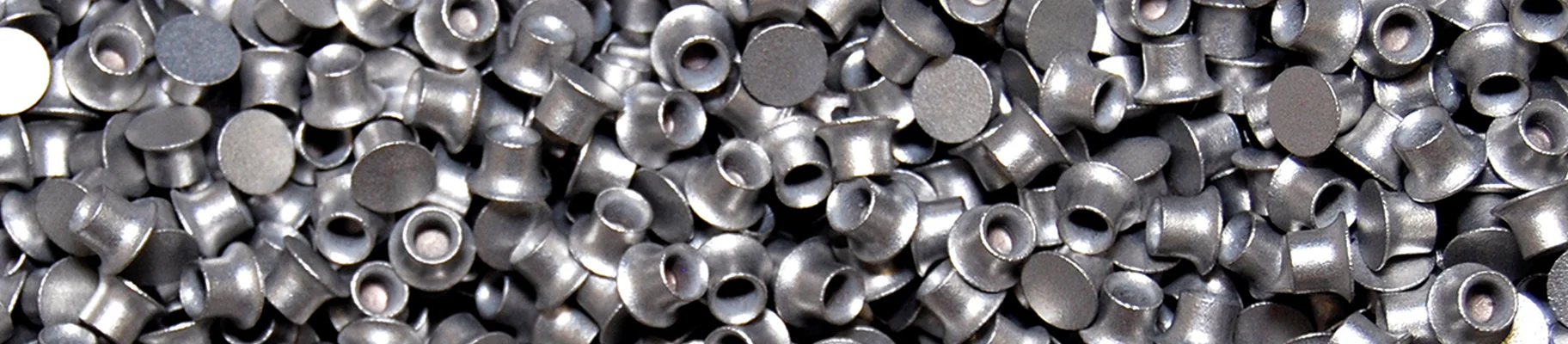
从瓶颈到突破:阿特拉斯-科普柯的3D 打印之旅
案例研究 | 阿特拉斯-科普柯
提高生产效率
增材制造 如何重新定义 Altas Copco 的效率、成本和生产速度
92 %的交付周期从 6-12 周缩短至 3-4 天
由于取消了外部供应商费用并减少了工时,生产成本节省了 30
材料浪费从约 7% 减少到接近零
提高应对计划外订单和客户紧急要求的灵活性
交货时间长、供应链中断和生产成本上升是现代制造业面临的共同挑战。传统方法往往难以满足对灵活性、速度和效率不断增长的需求。对于依赖外包部件的公司来说,延误和低效可能导致代价高昂的挫折和机会的丧失。
作为工业解决方案的领导者,阿特拉斯-科普柯在生产铆钉输送碗时面临着这些挑战,铆钉输送碗是汽车行业使用的自冲铆接系统中的重要部件。通过采用内部增材制造 (AM),该公司不仅克服了这些障碍,还节省了大量成本,减少了浪费,并大大缩短了交货时间。使用 EOS P 396和PA 2200聚合物材料,阿特拉斯-科普柯改变了生产方式。本案例研究探讨了增材制造 如何实现可衡量的改进并重塑其制造战略。
3D 打印 铆钉输送碗
"与 EOS 的合作为我们提供了交钥匙解决方案,并帮助我们调整了工艺流程,使我们现在能够批量生产多个组件,并正在快速制作数百个组件的原型,在短短 18 个月内就实现了投资回报"。
Jason Edwards,阿特拉斯-科普柯技术经理
挑战
传统上,阿特拉斯-科普柯依靠外部供应商提供铆钉输送碗等部件,而铆钉输送碗是汽车行业广泛使用的自冲铆接系统的关键部件。这种依赖导致交付周期延长至 6 至 12 周、生产成本增加以及供应链复杂化。此外,传统的生产工艺造成了约 7% 的材料浪费,凸显了对更具可持续性的解决方案的需求。
阿特拉斯-科普柯的技术经理 Jason Edwards 解释说:"我们希望更严格地控制生产,从而缩短交付周期,降低成本,并能够快速制作新产品的原型,"他解释说,"与 EOS 和 Additive Minds 的合作为我们提供了交钥匙解决方案,并帮助我们调整工艺,使我们现在能够批量生产多个组件,快速制作数百个新产品的原型,并在短短 18 个月内实现投资回报。
分类和进料
3D 打印 碗可有效输送铆钉,简化自动化生产流程
铆钉输送碗:阿特拉斯-科普柯汽车工业自冲铆接系统的关键部件
阿特拉斯-科普柯 IAS 英国有限公司是自穿刺铆接技术的市场领导者,这种基于铆钉的方法使汽车制造商无需焊接或预先钻孔即可轻松连接铝材或混合材料。
解决方案
为了应对这些挑战,阿特拉斯-科普柯与 EOS 及其咨询部门 Additive Minds 合作,将 AM 功能引入公司内部。他们选择了以灵活性和精度著称的EOS P 396 3D 打印机,并使用聚合物材料 PA 2200 制造铆钉输送碗。这一转变使阿特拉斯-科普柯能够精简供应链,减少对第三方供应商的依赖,并更严格地控制生产计划。内部 AM 方法还促进了快速原型制造,从而实现了快速迭代和设计优化。
EOS P3 NEXT
成果
向内部增材制造 的转变为阿特拉斯-科普柯带来了变革性的成果。其中最重要的改进之一是大大缩短了交货时间。以前,铆钉输送碗的生产需要 6 到 12 周的时间,这主要是由于对外部供应商的依赖和传统制造工艺的复杂性造成的。使用EOS P 396 3D 打印机后,交货时间缩短至 3 至 4 天,显著缩短了 92%。这一改进可以更快地响应生产需求,并更灵活地满足客户的紧急要求。
节约成本是另一项重要成果。阿特拉斯-科普柯通过消除对外部供应商的需求、减少工时以及简化整体生产流程,使生产成本降低了 30%。增材制造 的效率最大限度地降低了与换装、设置更改和供应链管理相关的费用。此外,AM 工艺的精确性和可靠性大大减少了材料浪费。传统制造方法会造成约 7% 的材料浪费,而新工艺则将这一数字降至近乎零。这种减少不仅有助于提高成本效益,还通过最大限度地减少资源消耗支持了可持续发展目标。
通过采用增材制造,阿特拉斯-科普柯提高了生产的灵活性、成本效率和环境效益--证明了 AM 在工业应用中的强大潜力。"AM对我们来说是一个变革。我们在全球范围内赢得了新的合同,因为我们可以直接供货,成本更低,交货时间更短。阿特拉斯-科普柯的技术经理 Jason Edwards 总结说:"EOS 是我们的合作伙伴,它在我们的转型过程中一直支持我们,为我们提供快速支持,并不断为我们的部件设计提供建议,使我们的3D 打印机达到最佳效果。
高效可靠
转向内部3D 打印 意味着阿特拉斯-科普柯需要更少的第三方组件,不再受供应链交货时间和运输延误的限制。
配备3D 打印机EOS P 396阿特拉斯-科普柯生产车间
阿特拉斯-科普柯团队
增材制造 为我们带来了变革。我们在全球各地赢得了新合同,因为我们可以直接供货,成本更低,交货时间更短。
Jason Edwards,阿特拉斯-科普柯技术经理
EOS 成功案例
通过 EOS 探索三十年来开拓3D 打印的卓越成就